Ceramic Coating Services
Ceramic coating is a state-of-the-art process that involves applying a thin liquid layer over a surface, which is then cured to form a tough, resilient, and sleek protective coating. It’s distinct from powder coating in that it's applied as a liquid. Ceramic coating is renowned for its exceptional high-temperature resistance and is often used for components that are subjected to extreme heat. Moreover, it offers notable corrosion resistance, making it ideal for a multitude of applications.
Ceramic Coating Benefits

.png)

Enhanced Protection
Ceramic coating offers a strong protective layer, shielding the surface from UV rays, scratches, chemicals, and contaminants.

Corrosion & Oxidation Resistant
Prevents metal surfaces from oxidizing and corroding, especially in environments with salt or humidity.

Colour Versatility
An endless spectrum of colours and effects with options for textures like matte, gloss, or hammer-tone.

Eco-Friendly
Ceramic coatings are more environmentally friendly compared to traditional coatings, as they last longer & reduce the usage of cleaning chemicals.

Hydrophobic Properties
Ceramic coating repels water effectively, ensuring that water beads up and rolls off, taking dirt and grime with it.
.png)
Ceramic Coating Process
1
Degreasing
Parts that are to be coated are meticulously cleaned and degreased. This is crucial to remove any surface contaminants such as oils, grease, and dirt, which might interfere with the adhesion of the ceramic coating.

2
Outgassing
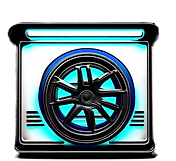
The parts are placed in an oven and heated to high temperatures. This process, known as outgassing, draws out any residual oils and contaminants within the metal itself, ensuring an immaculate surface for coating.
3
Masking

To make sure that certain areas remain free of coating, masking is done. This involves covering areas that should not be coated with tape, plugs, or other materials to shield them during the application process.
4
Sandblasting

The surface of the parts is then blasted with abrasive materials such as aluminum oxide. This creates a rough texture, which helps in ensuring that the ceramic coating adheres effectively to the surface.
5
Spraying

This is the final step where the ceramic coating is applied to the parts. A specialized spray gun is used to evenly apply the coating. This not only enhances the appearance of the parts but also adds a protective layer.